Comprehensive Guide: What is Porosity in Welding and Just How to avoid It
Porosity in Welding: Identifying Common Issues and Implementing Best Practices for Avoidance
Porosity in welding is a prevalent problem that often goes undetected until it causes significant troubles with the integrity of welds. This typical problem can endanger the stamina and longevity of bonded structures, posturing safety threats and bring about pricey rework. By understanding the origin of porosity and carrying out reliable prevention strategies, welders can substantially improve the high quality and reliability of their welds. In this discussion, we will discover the crucial variables adding to porosity development, analyze its damaging results on weld efficiency, and talk about the best practices that can be taken on to decrease porosity occurrence in welding processes.
Usual Reasons For Porosity
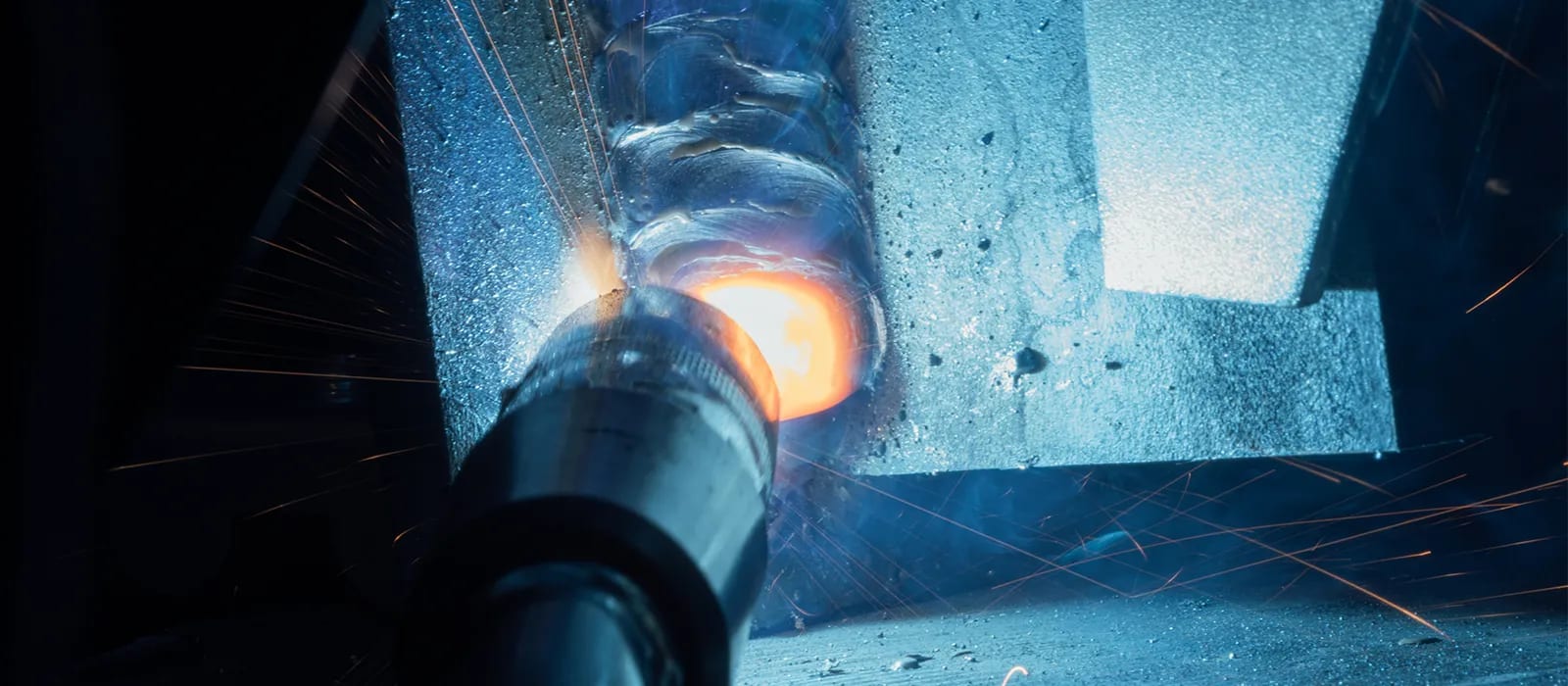
Utilizing unclean or wet filler products can introduce contaminations into the weld, adding to porosity problems. To minimize these usual causes of porosity, complete cleaning of base steels, correct securing gas selection, and adherence to optimum welding parameters are important techniques in attaining high-quality, porosity-free welds.
Impact of Porosity on Weld Top Quality

The visibility of porosity in welding can significantly compromise the architectural integrity and mechanical residential properties of bonded joints. Porosity creates gaps within the weld steel, deteriorating its total stamina and load-bearing ability. These spaces function as tension concentration points, making the weld extra susceptible to cracking and failure under applied tons. Additionally, porosity can lower the weld's resistance to rust and various other environmental variables, additionally decreasing its longevity and performance.
Welds with high porosity levels often tend to display reduced impact stamina and decreased capacity to deform plastically before fracturing. Porosity can restrain the weld's capacity to efficiently transfer forces, leading to premature weld failing and prospective safety threats in vital frameworks.
Ideal Practices for Porosity Avoidance
To enhance the structural integrity and quality of welded joints, what particular steps can be implemented to decrease the incident of porosity throughout the welding process? Porosity avoidance in welding is essential to make sure the honesty and strength of the final weld. One reliable practice is appropriate cleansing of the base steel, removing any kind of pollutants such as rust, oil, paint, or dampness that might result in gas entrapment. Making certain that the welding tools remains in great condition, with clean consumables and suitable gas flow prices, can also significantly decrease porosity. Furthermore, preserving a secure arc and regulating the welding parameters, such as voltage, existing, and travel speed, helps produce a constant weld Discover More swimming pool that lessens the danger of gas entrapment. Utilizing the appropriate welding strategy for the specific material being welded, such as readjusting the welding angle and gun position, can better avoid porosity. Regular inspection of welds and instant removal of any concerns recognized throughout the welding procedure are necessary practices to avoid porosity and produce high-grade welds.
Importance of Appropriate Welding Methods
Applying proper welding see this here strategies is vital in guaranteeing the architectural honesty and high quality of welded joints, constructing upon the foundation of reliable porosity prevention actions. Extreme heat can lead to enhanced porosity due to the entrapment of gases in the weld swimming pool. Additionally, making use of the ideal welding criteria, such as voltage, present, and travel speed, is important for attaining audio welds with marginal porosity.
In addition, the selection of welding process, whether it be MIG, TIG, or stick welding, should line up with the particular needs of the job to make certain ideal outcomes. Correct cleaning and prep work of the base metal, along with choosing the ideal filler product, are likewise essential components of skillful welding methods. By sticking to these ideal techniques, welders can minimize the danger of porosity formation and create premium, structurally sound welds.

Examining and Quality Control Procedures
Quality assurance measures play a crucial function in validating the honesty and integrity of bonded joints. Checking treatments are important to identify and stop porosity in welding, making certain the stamina and resilience of the last product. Non-destructive screening techniques such as ultrasonic testing, radiographic screening, and visual evaluation are typically used to recognize prospective problems like porosity. These techniques allow for the assessment of weld top quality without endangering the honesty of the joint. What is Porosity.
Post-weld inspections, on the various other hand, assess the final weld for any kind of issues, consisting of porosity, and validate that it satisfies specified standards. Implementing a detailed top quality control plan that consists of comprehensive testing procedures and inspections is paramount to lowering porosity concerns and ensuring the total high quality of welded joints.
Verdict
Finally, porosity in welding can be an usual problem that affects the quality of welds. By recognizing the usual reasons of porosity and implementing finest methods for avoidance, such as correct welding strategies and screening actions, welders can ensure high top quality and reliable welds. my sources It is important to prioritize prevention techniques to minimize the event of porosity and preserve the integrity of bonded frameworks.